Learning About Motor Felt Wicks
There has been much talk about motor lubricating lately, including many that are advocating not lubricating the motor at all. I am not sure where this advice started, whether it began because the later white Featherweight motors do not have lubricating ports, or if it was from those warning against using sewing machine oil in your motor. (To be sure, sewing machine oil should never be put inside a motor, because oil will destroy it.) Regardless of where the advice started, not lubricating any motor that was designed to be lubricated is very bad advice.
There are two places that were made for lubricating on all black and tan Featherweights motors as well as a few of the early model white Featherweights. Note the locations in the photos provided, of the two lubricating ports/tubes found on the motor of your Singer Featherweight.

If you have a white Featherweight, and the ports are nowhere to be found on your motor, then you have a later model with a different style of bushing in the motor that did not require lubricating.

The lubrication ports/tubes have a felt wick inside that extends to approximately 3/8 of an inch from the top of the tube all the way down to the shaft of the motor itself. The following photo shows one of the felts after being removed from the port so you can see the length of the felt wick itself.

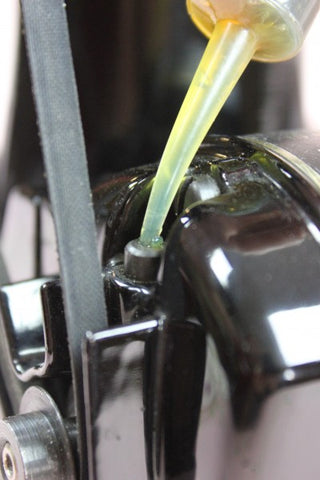
As the photo shows, push lubricant from the lubricant syringe into the ports until it is full to the port opening. Because the wick goes almost the full length of the tube, it will only hold a small amount of lubricant.

If the tube/ports already seem full of old hard lubricant you can carefully remove it with a toothpick, or by using the hollow port cleaning tool (included with the motor lubricant we carry). Just be careful not to force the toothpick down the tube past the point of resistance from the interior felt wick.

If your Featherweight has not been used for a long time or has not been serviced regularly, the felt can become very hard and will stop wicking the new lubricant down to the shaft of the motor. But the good news is this can be easily remedied. The fastest and easiest way to accomplish this is by using a hairdryer (don’t use your wife’s good one, or she may need it just about the time you go to use it!) to blow hot air into the motor port/tube while running the motor, either with the belt off or with the stop-back motion knob released (as if you were winding a bobbin). Let the motor run at full speed until the heat from the hairdryer melts the old lubricant within the wick and thus starts the lubricant flowing to the shaft of the motor. You will usually hear a change in the sound of the motor once the lubricant reaches the shaft and the speed should increase as well. This process could take up to ten minutes.
If you happen to open your motor for any reason, be careful when reassembling the motor that you do not push the felt wick out the end of the motor housing, as shown in the following photo.

These are extremely difficult to replace. So, if your wick is shown slipping down like that above, then use a stiletto or long needle to push it back up inside.

On a side note, the motor that was used in this photo had sat unused for so long that part of the felt wick was attached to the shaft of the motor itself, almost as if it was glued on there. It easily buffed off the shaft, but it was indicative of a motor that had not been operated for many years or even decades. So, definitely lubricate your motor on a regular basis – about once or twice per year depending on how often you use it. Finding proper motor lubricant can be a very opinionated topic in some circles. Well, the key is the proper low melting point. Click here for more information and to see a video time-lapse comparing all lubricants found on the market today.
If you have any questions about getting your motor lubricated, send me an e-mail or give me a call – glad to assist you anytime.